AI in Factory Automation
Factory automation loves buzzwords and none is more popular than Artificial Intelligence. However, it’s rarely discussed what this will mean in practice. When people say Artificial Intelligence, they often are referring to Machine Learning, a subset of AI that allows a computer program to learn and improve over time.
Machine Learning means using algorithms to leverage data and improve performance. There are many algorithms to accomplish this, but Neural Networks seem primed to dominate the manufacturing industry in the near future.
Neural Networks
Neural networks are a powerful computing system that is ideal for creating predictive models based on complex relationships between large amounts of input data. They are used in complex, data-heavy problems like facial recognition, cancer diagnostics, stock market analysis, and many more. Here is a simple overview of how they work.
Neural networks essentially replicate the human brain by having layers of “neurons”. They take in a huge amount of input data that is fed into each neuron in the “hidden layers” which have a specific weight. These neurons eventually funnel together to select an outcome node. As the neural net learns, the weights of the hidden layer are adjusted to make accurate predictions.
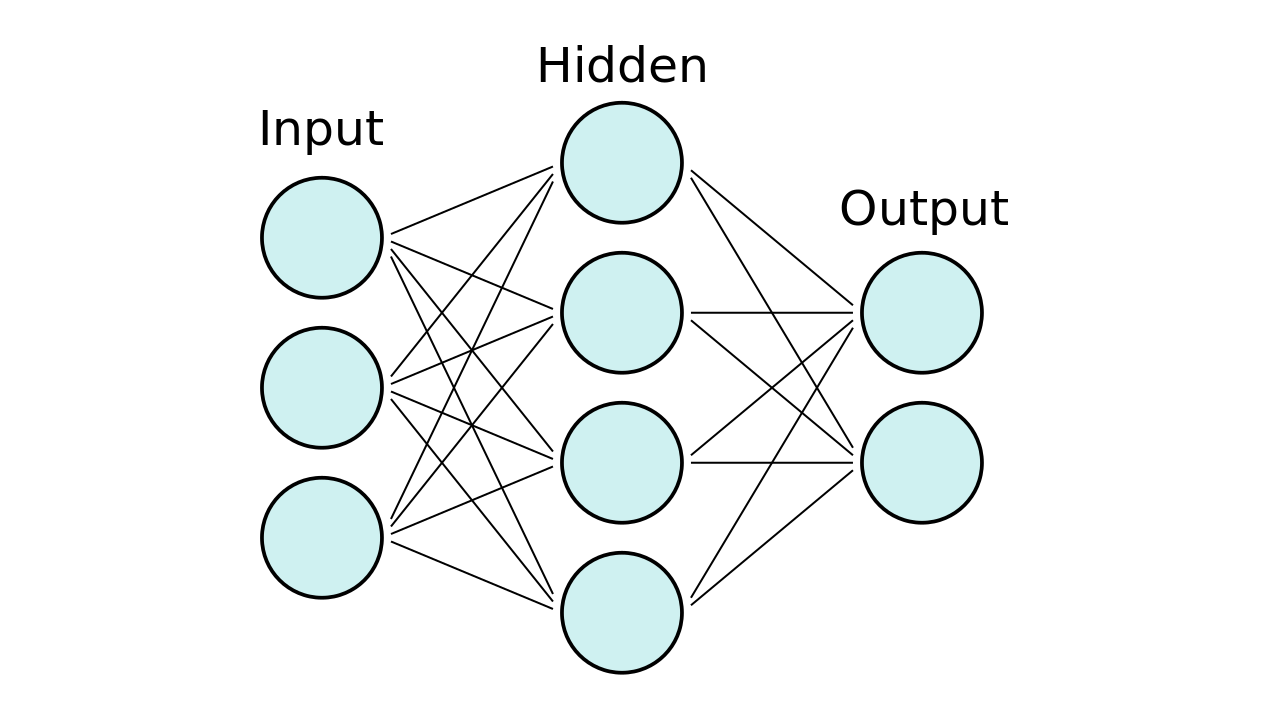
Here is a great video made by Simplilearn that gives an explanation of neural nets:
Why Neural Networks Are Inevitable in Factory Automation
Massive Upside:
The typical advantages of neural nets are so well suited to manufacturing that they are impossible to ignore. The predictive power of neural nets means that they would be extremely valuable for predictive maintenance, improving quality and yields of a process, reducing energy and resource requirements, and helping manage the supply chain. These advantages can be easily quantified and given a dollar value, which will help drive the growth of neural nets in manufacturing.
Limited Downside in Manufacturing:
Neural nets do carry some negatives, however they are well mitigated by the scale of the manufacturing industry. The three main downsides are:
1. Large amounts of data is required
Although we as an industry don’t do a great job of collecting large amounts of data, manufacturing creates a tremendous amount of data and data availability should be a non-issue in the future as we progress towards Industry 4.0.
2. Computationally expensive
Given the ethernet based architecture of modern manufacturing, all the data can easily be stored and analyzed remotely. On-site computational power would be minimal and the cost of running remote servers would be negligible compared to the extreme benefits offered by neural nets.
3. Neural nets are a “Black Box”-- We don’t know why they make the predictions that they do
This issue will not immediately hinder the growth of neural nets in manufacturing, but it will be hugely impactful for the future of manufacturing and should be thought about carefully and with practical foresight.
Why is the "Black Box" an Issue?
Neural nets are trained using some predefined output or accuracy threshold designated as a “success”. When creating a predictive model, it sometimes does not matter how the model is able to make successful predictions. For example in computer vision, we don’t really care how a computer knows that a stop sign is a stop sign, so long as it never makes a mistake.
Although, in some instances, such as cancer diagnostics, the “why” is a real issue. Neural nets are great for cancer diagnostics because in order to make a successful diagnosis, the input requires such a large amount of data with complex relationships. However, it would be great to know why the diagnosis is being made so that humans could take preventative measures to reduce the risk of cancer.
Manufacturing suffers from something similar, predictive maintenance is great for reducing downtime, but it would be ideal to know why a component is failing. It seems inevitable that we will use the neural nets to advise how to build longer lasting components, or improve yield, or reduce energy usage, but we won’t know exactly why the computer makes these decisions.
How Will the "Black Box" Impact the Future of Engineering
To recap, neural nets are trained with a large amount of historic input and output data. The neural net creates a model to predict the output, then uses the historic data to judge if it was successful and refine the model. Let's imagine an example where you feed a neural net historic data such as the component's age, materials of construction, typical daily usage, environmental conditions and finally when that component failed. The neural net would ingest all this data and create a predictive model for when a component will fail.
Eventually, this model would be quite accurate at predicting component failure. However we would not know exactly why. Engineers would use this model to improve on the design and improve component lifespan.
Where this could be an issue:
In this example, innovation is purely result driven. Rather than the typical research and development cycle of iterative failure mirorring the scientific method, we will now always be chasing short term improvements. This will lead us to squeeze all the progress out of small scale innovations, but we may miss the larger scale innovations because we lack a broader understanding of why the design is improving.
My fear is that the "Black Box" of neural nets will do the 21st century equivalent of improving the steam engine without developing electromagnetic motors. They will miss the massive breakthroughs that come from broad, theoretical understanding. Secondly, neural nets will also pursue constant improvements to our success criteria and I have doubts that we can be flexible enough in defining that success criteria moving forward.
Two Things We Must Consider with Manufacturing Artificial Intelligence
1. Having a long time horizen for innovation
To avoid the problems mentioned above we must not just focus on short term improvements. A short time horizon is consistently a problem in the manufacturing industry due to the small margins and heavy capital investments. However, if we allow our research and development to be dictated by short term gains brought on by neural nets, we will never make the massive breakthroughs necessary for advancement.
2. Managing the definition of success in our models
If simply predicting component failure or improving yield is the success criteria of our models, they will only aim to acheive those goals. It is ethically and financially important that we reinforce the neural networks on criteria such as safety, environmental impact, and other tough-to-quantify aspects that we should strive to value as a society.
Don't get me wrong, artificial intelligence in the form of neural nets will be a huge boon to manufacturing. However, the industry seems systemically unprepared and thoroughly unaware of the impact it will have and how to manage it. Industry 4.0 will require more than a shift in techonlogy, but a paradigm shift that is not typical of our industry.